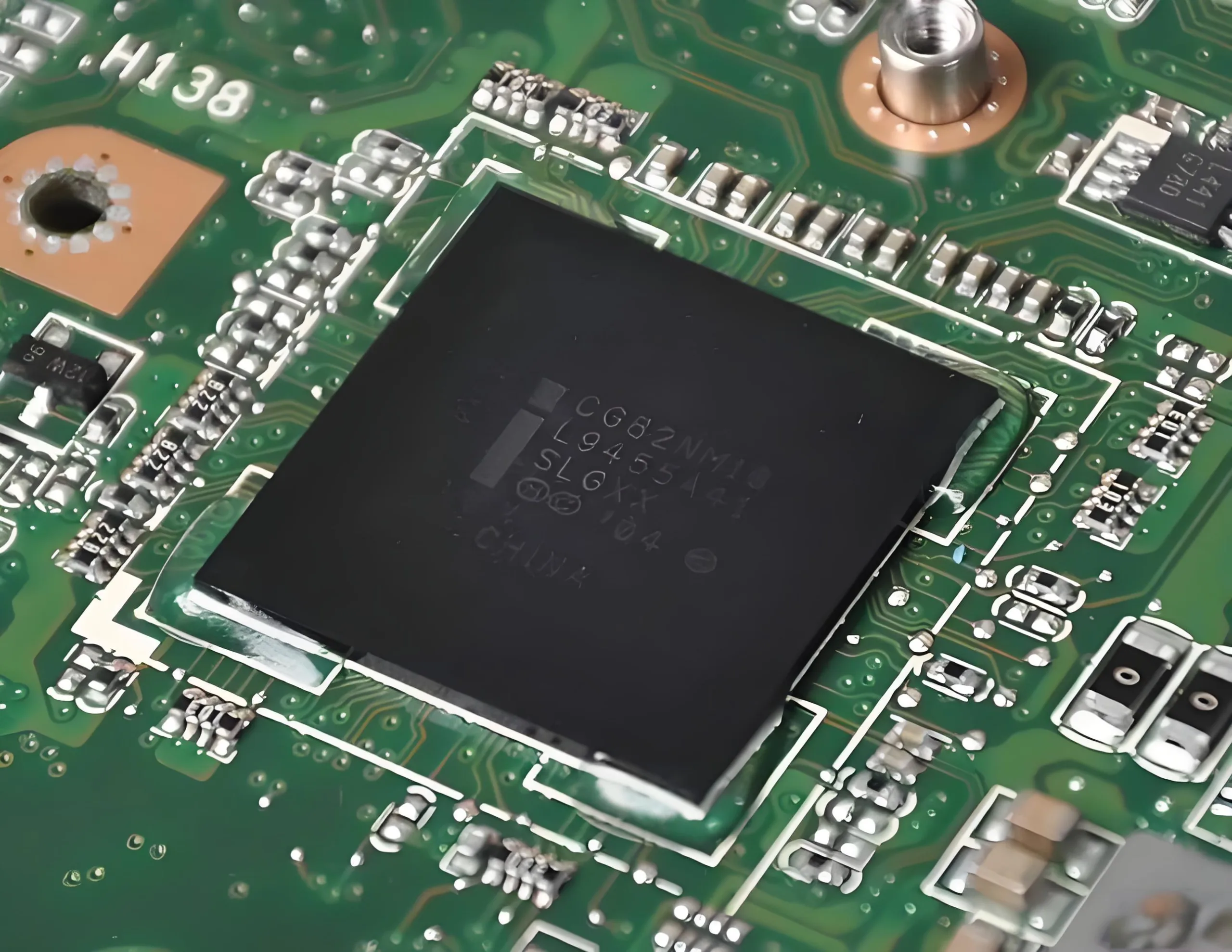
BGA void control
In the world of precision PCB manufacturing, every detail is crucial, especially when it comes to BGA (Ball Grid Array) packaging. BGA voids, or tiny cavities inside solder balls, may seem insignificant but can hide major risks affecting product reliability. This article will delve into how to reduce the occurrence of BGA voids through meticulous process control, ensuring the stability and safety of electronic connections.
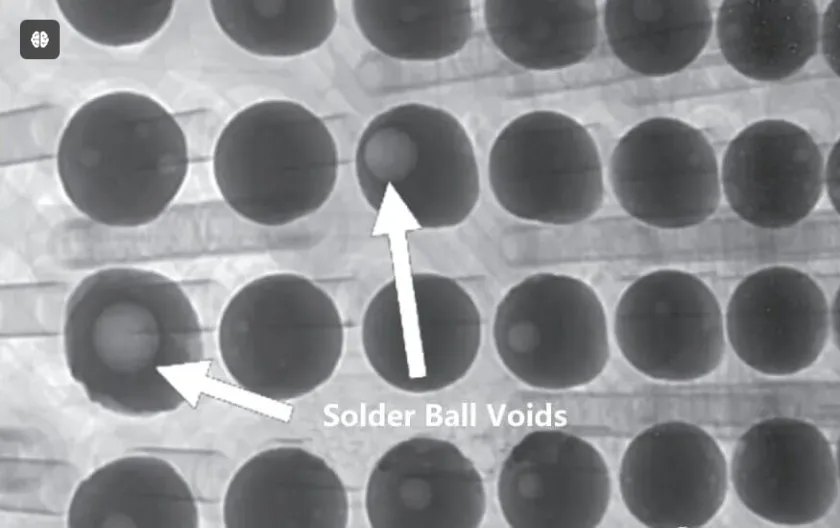
BGA Void
The Location of Voids: The Key Point
أولاً, let’s clarify one thing: not all voids are equally dangerous. Voids inside solder balls, if they do not pose a direct threat to structural integrity, may have limited impact. لكن, when voids appear at the interface between the solder ball and package substrate or the solder ball and PCB, the situation is drastically different. These interface voids act as potential crack accelerators; once subjected to external forces, they can lead to solder joint cracks, severely affecting product reliability and lifespan.
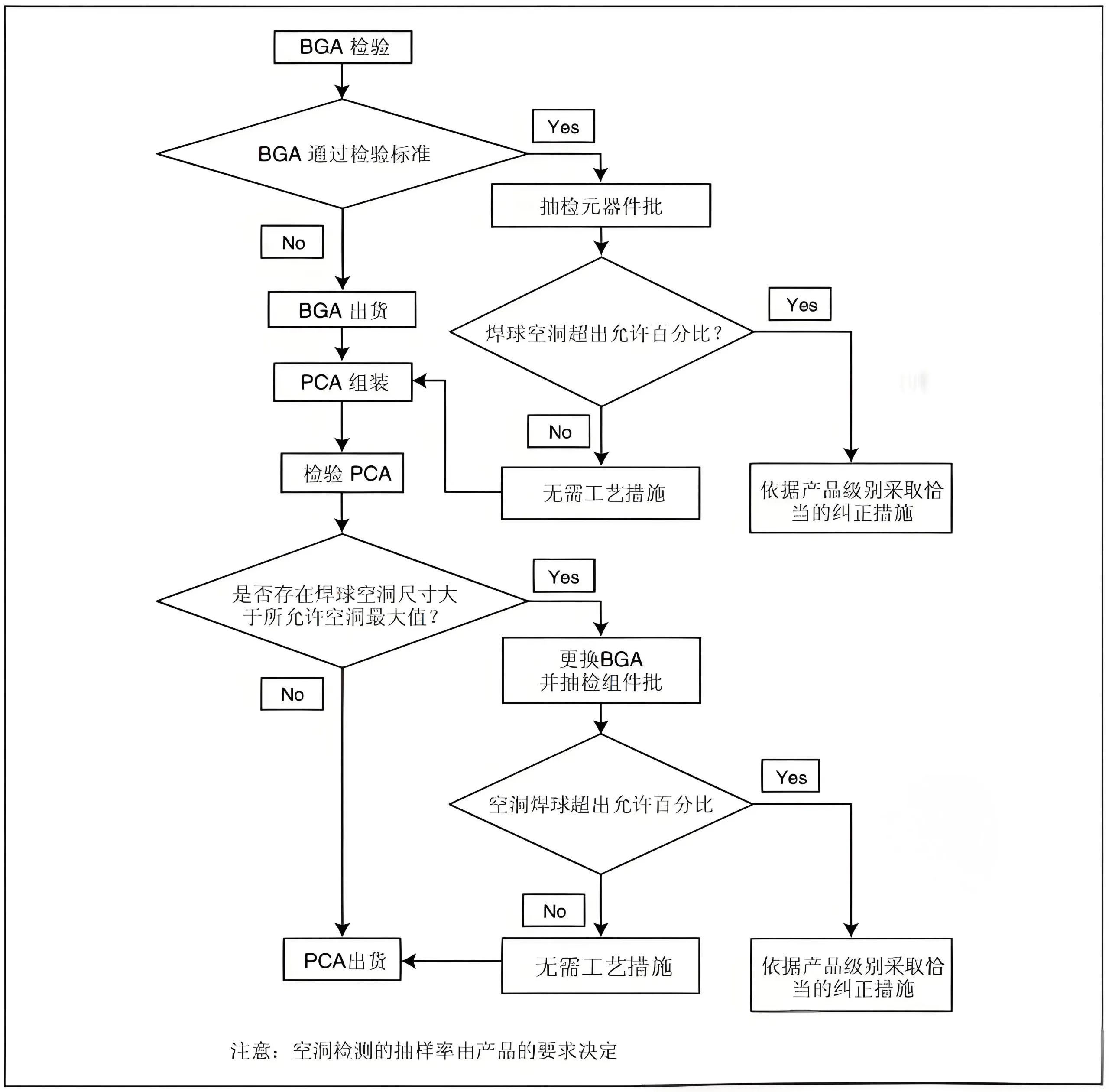
Flowchart of Void Assessment
To intuitively understand the void assessment process, we introduce Figure A-1. This flowchart details every step from void identification to taking corresponding actions, serving as an effective tool for ensuring process control.
Corrective Measure Indicators: Precise Actions
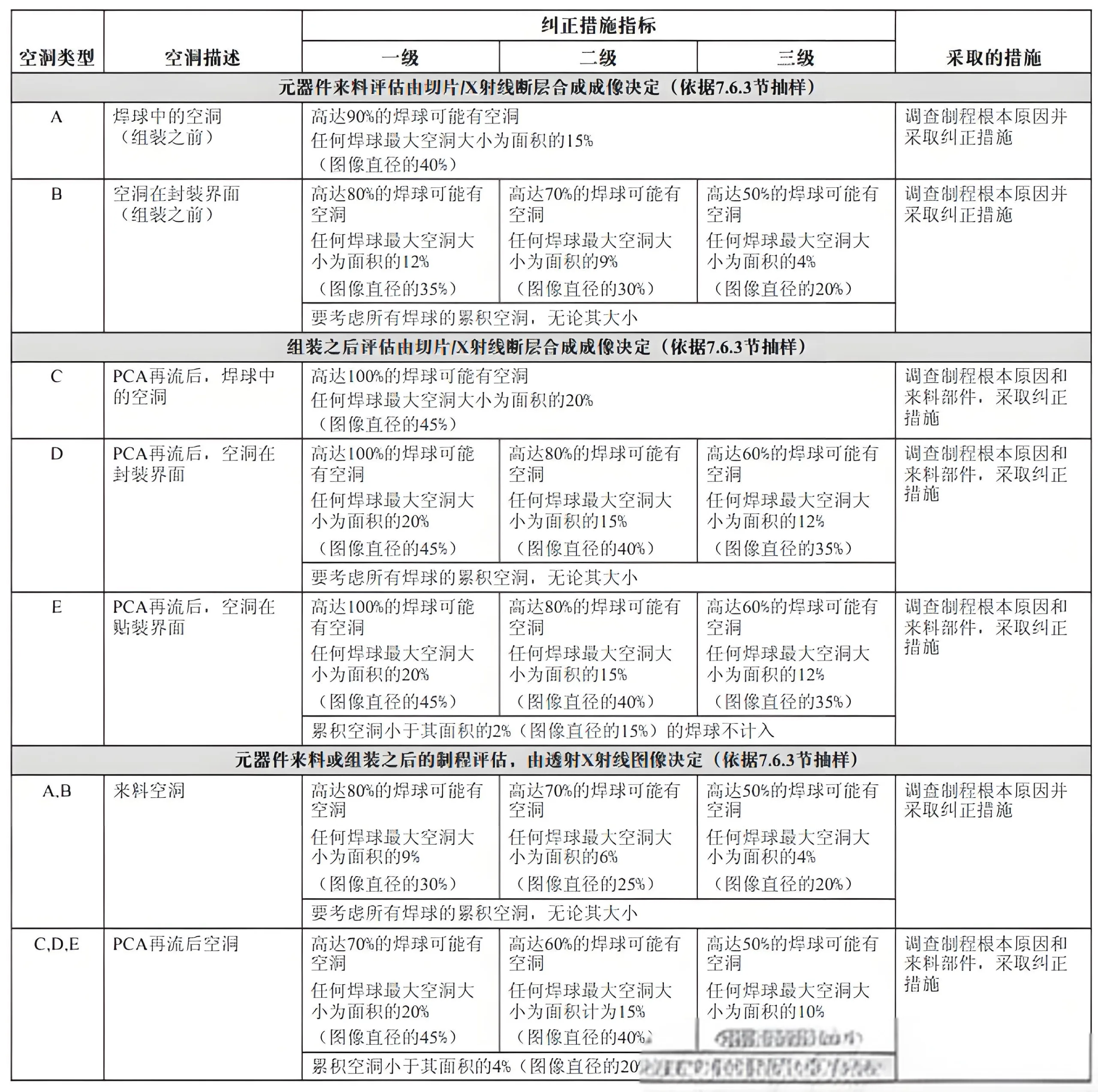
A-1 Corrective measure index for connecting plates used with 1.5, 1.27 or 1.0mm pitch
For BGAs with different pitches, we have developed detailed corrective measure indicators, as shown in Tables A-1 to A-3 (the content of which is summarized here in text form). Based on IPC standards, these tables combine void location, size, and quantity to provide specific action guidelines for BGAs of different pitches. على سبيل المثال, Table A-1 lists recommended measures for different types and quantities of voids for BGAs with pitches of 1.5mm, 1.27مم, and 1.0mm, aiming to maintain connection reliability.
Process Characteristic Description: Scientific Control
Process characteristic description is at the core of reducing voids. Based on void size and following the suggestions in the flowchart, combined with the three-tier structure in IPC standards, it considers void location, size, and quantity to establish necessary control measures. These measures apply not only to continuous optimization of existing products but also to new product introductions, product and process qualifications, equipment setup changes, component qualifications, and customer feedback responses.
Challenges and Responses to Fine-Pitch BGA
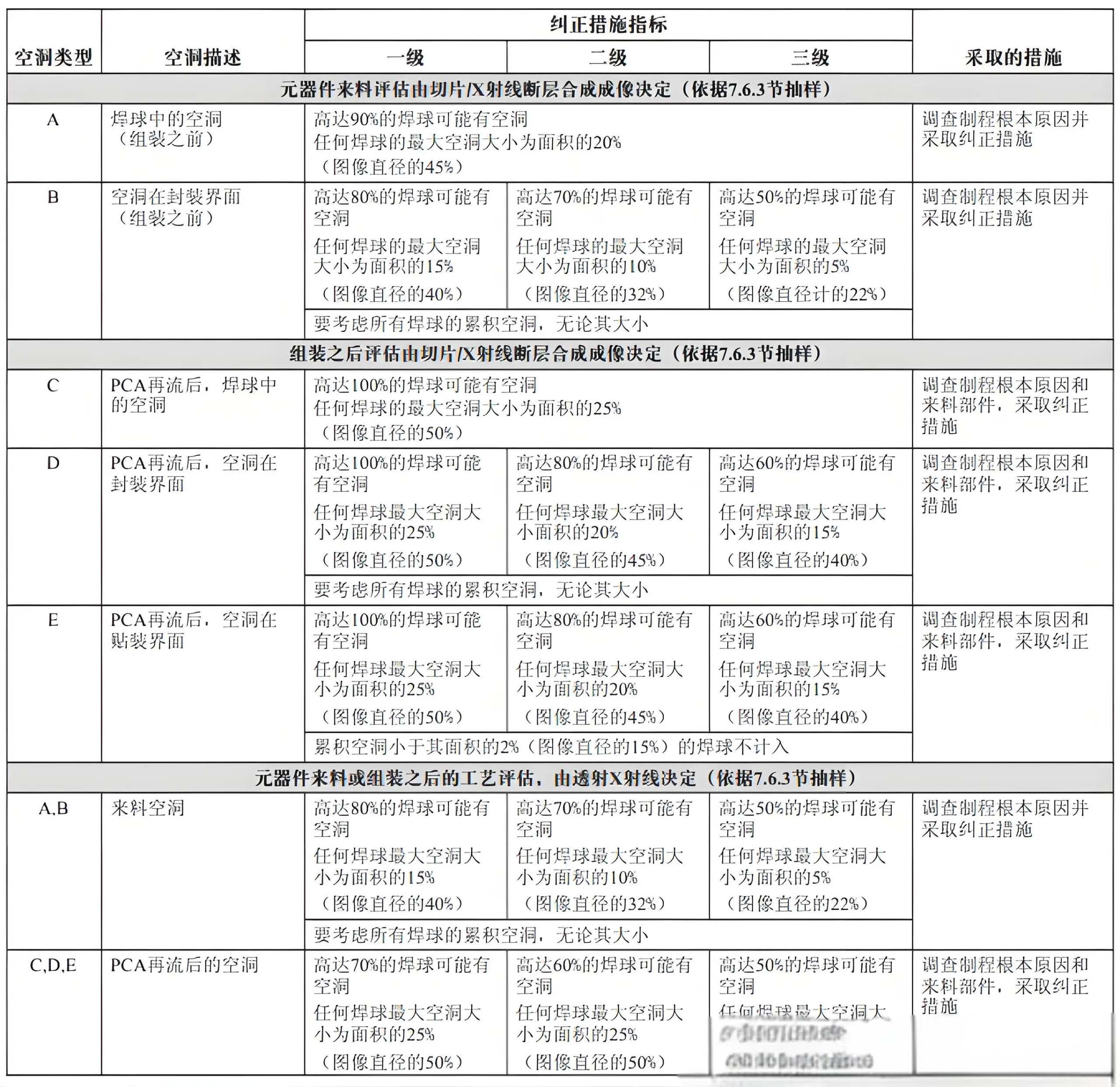
A-2 Corrective measure index for connecting plates used with 1.5, 1.27 or 1.0mm pitch
As BGA pitch continues to decrease, so does the connection area, posing higher demands on void control. Table A-2 specifically addresses BGAs with pitches of 0.8mm, 0.65مم, and 0.5mm, providing detailed corrective measures. For fine-pitch BGAs, even minor voids can significantly affect connection reliability. لذلك, stricter control measures, such as reducing void size, must be taken to compensate for the decreased connection area.
Via-in-Pad Design and Void Control
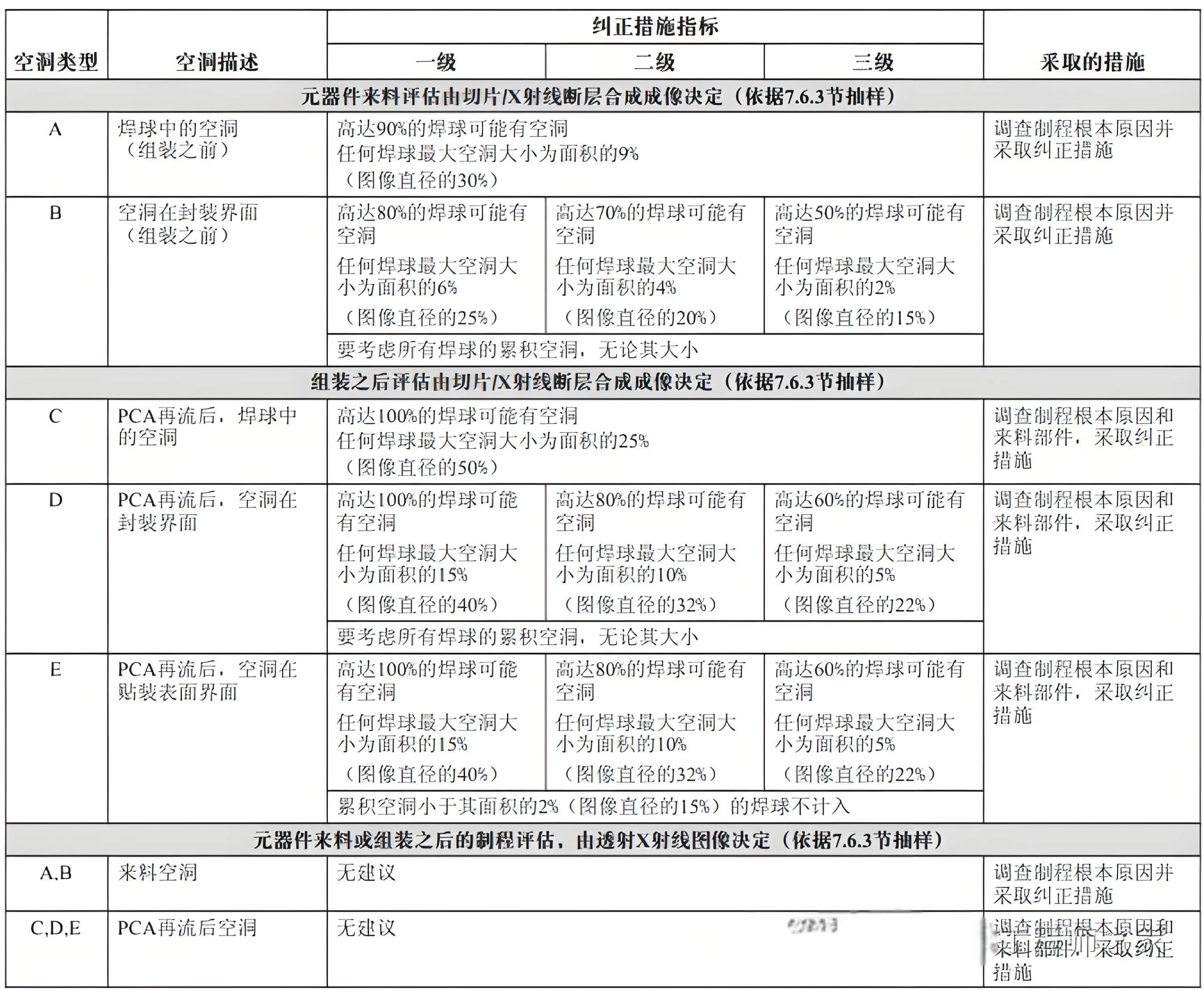
A-3 Corrective measure index for connecting plates used with 1.5, 1.27 or 1.0mm pitch
In designs with smaller pitches, microvias and via-in-pad designs become key to obtaining sufficient routing space. لكن, this introduces new challenges: how to ensure these designs do not increase the risk of voids? Figure A-2 (imagine a schematic showing how cracks can propagate from voids) demonstrates how voids can affect solder joint reliability. To avoid this, via-in-pad designs require further restrictions on void tolerances, as shown in Table A-3.
Void Process Control Standards
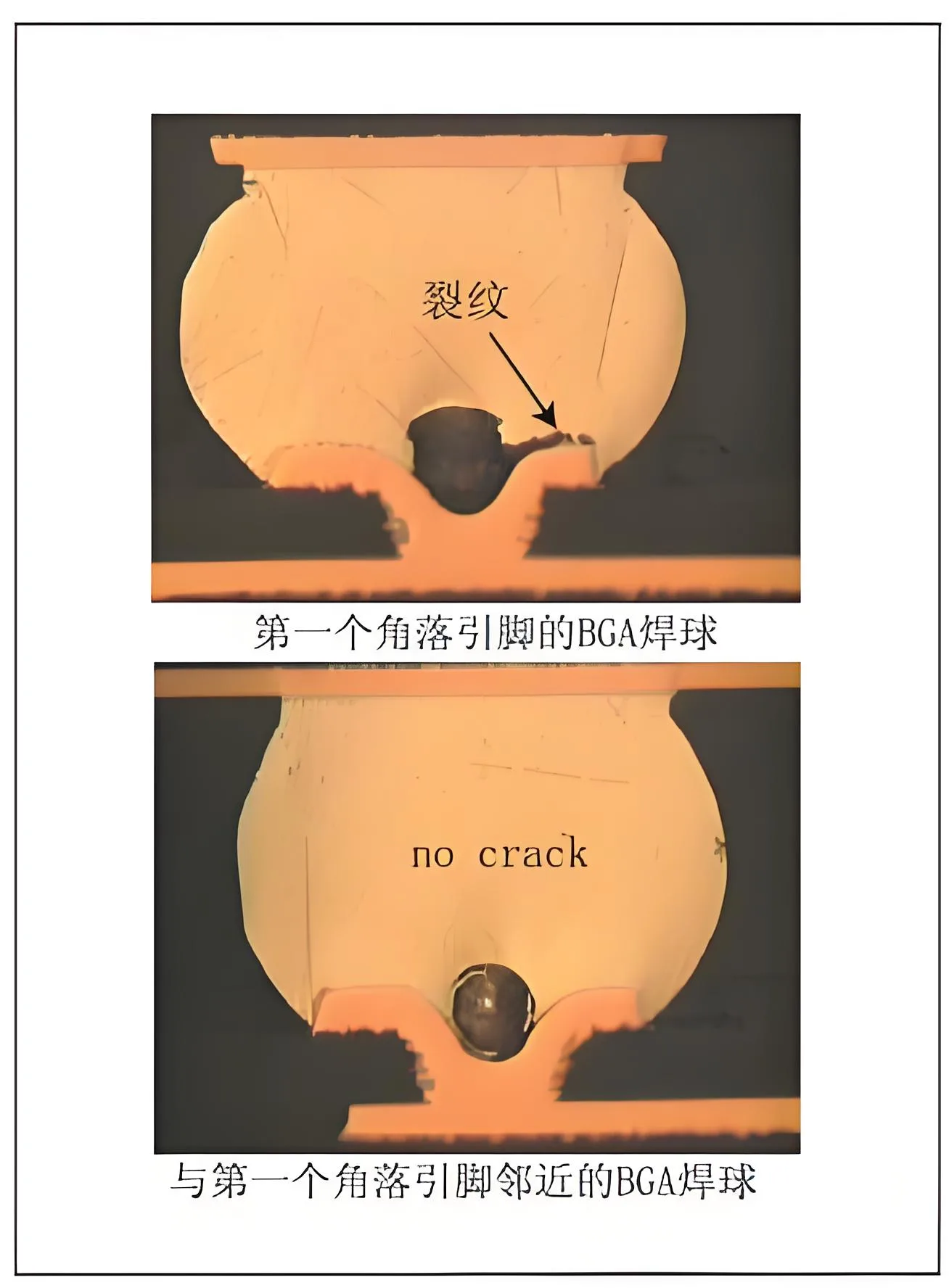
Void in BGA
The size and number of voids are important indicators for evaluating the effectiveness of process control. Routine occurrence of voids indicates a loss of process control, necessitating necessary tools to improve processes and materials. Based on size and pitch, we define acceptable characteristics of voids to ensure the reliability of the final product.
Details Determine Success or Failure: Consideration of Solder Ball Shape
Lastly, the impact of solder ball shape on void control cannot be ignored. In collapsed solder balls, the ball becomes ellipsoidal rather than a uniform sphere, leading to a solder joint diameter at the ball center that is usually larger than the diameter from the ball to the connection pad interface. This shape change affects the size and distribution of voids, hence, when setting standards, different combinations of solder ball and connection pad sizes must be considered.
خاتمة: The Fusion of Art and Science
Reducing BGA voids through process control is a fusion of art and science. It requires both profound knowledge in electronic engineering and meticulous craftsmanship. Through precise actions and scientific control, we can effectively reduce the occurrence of voids, ensuring the stability and safety of electronic connections. In this challenging and opportune era, let us work together to explore more unknowns, create more reliable electronic products, and contribute to human technological progress.