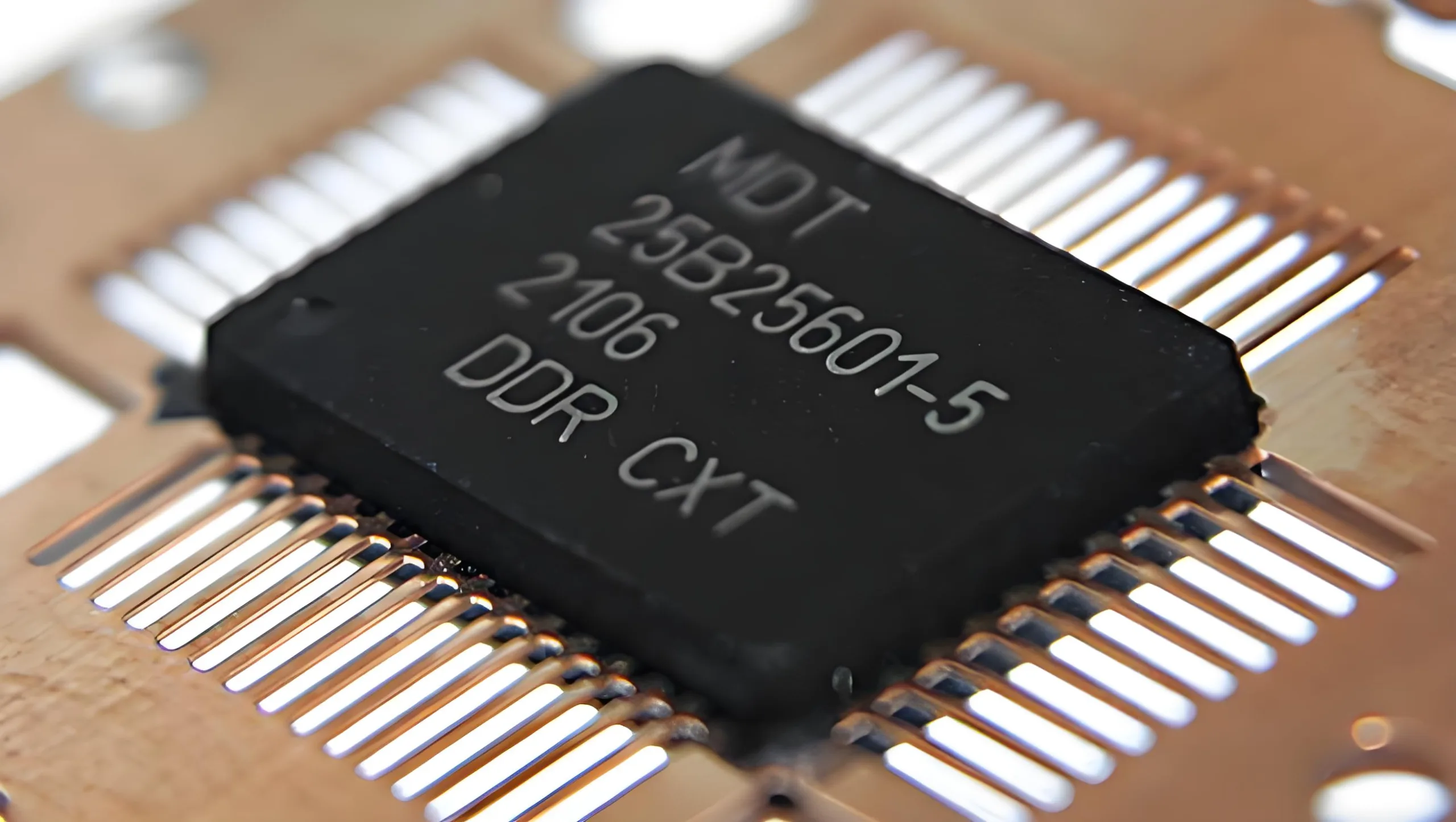
PCB inkjet printing technology
In the precise world of electronics, cartes de circuits imprimés (PCB) serve as the nervous system for electronic devices. Innovations in PCB manufacturing technology directly impact the future of the entire electronics industry. Among these innovations, inkjet printing technology stands out for its unique appeal, particularly the thermal bubble and piezoelectric inkjet technologies, which are leading PCB manufacturing towards higher levels of precision and efficiency. This article will delve into the working principles, characteristics, and applications of these two inkjet technologies in PCB manufacturing. Through comparative analysis, it reveals how they collectively shape the new future of PCB manufacturing.
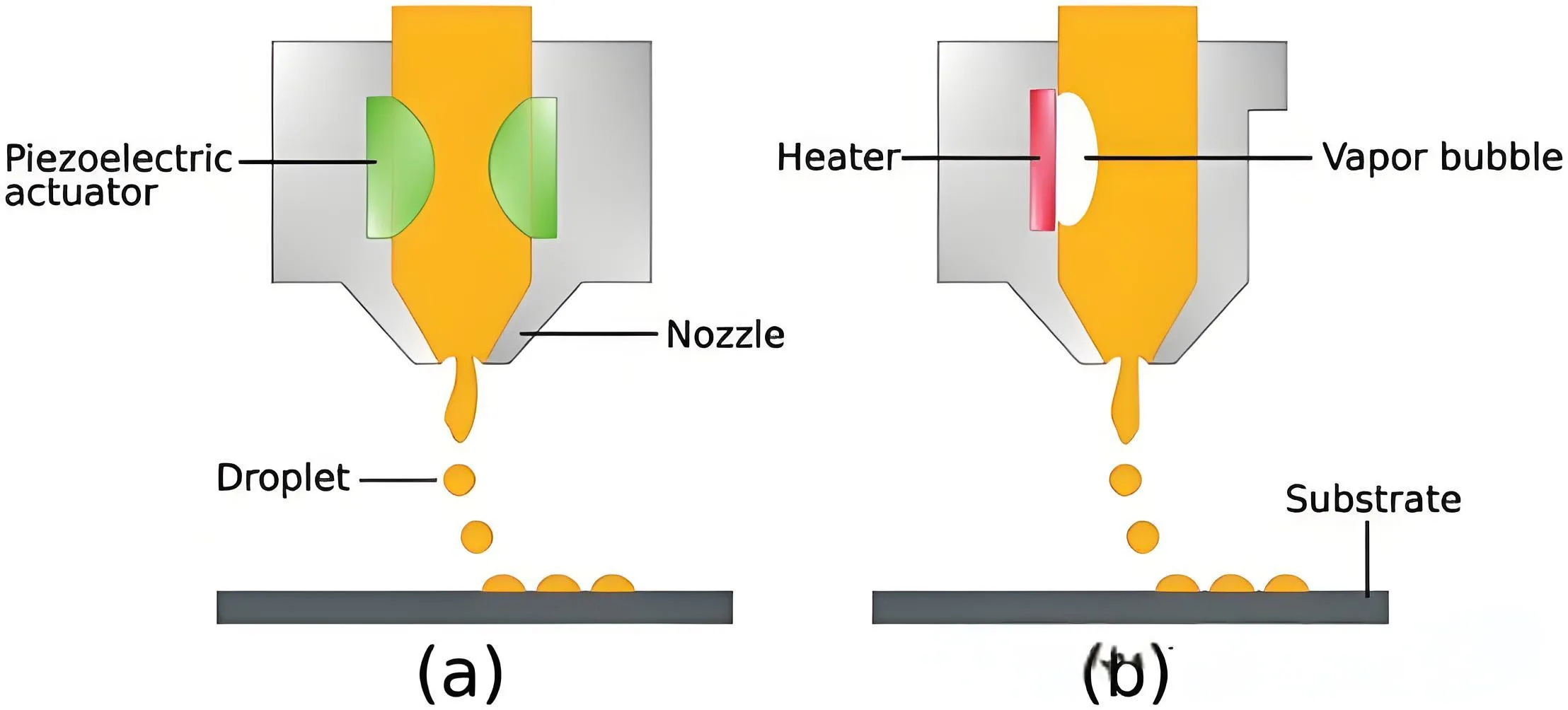
The principle of PCB inkjet printing technology.
On-Demand Inkjet: The Dual Wings of Technology
The core of inkjet technology lies in on-demand jetting, which precisely controls the ejection of ink droplets to achieve accurate printing of patterns or circuits. Thermal bubble and piezoelectric inkjet technologies, as two mainstream technologies, operate on fundamentally different principles yet each has its advantages.
Thermal inkjet technology
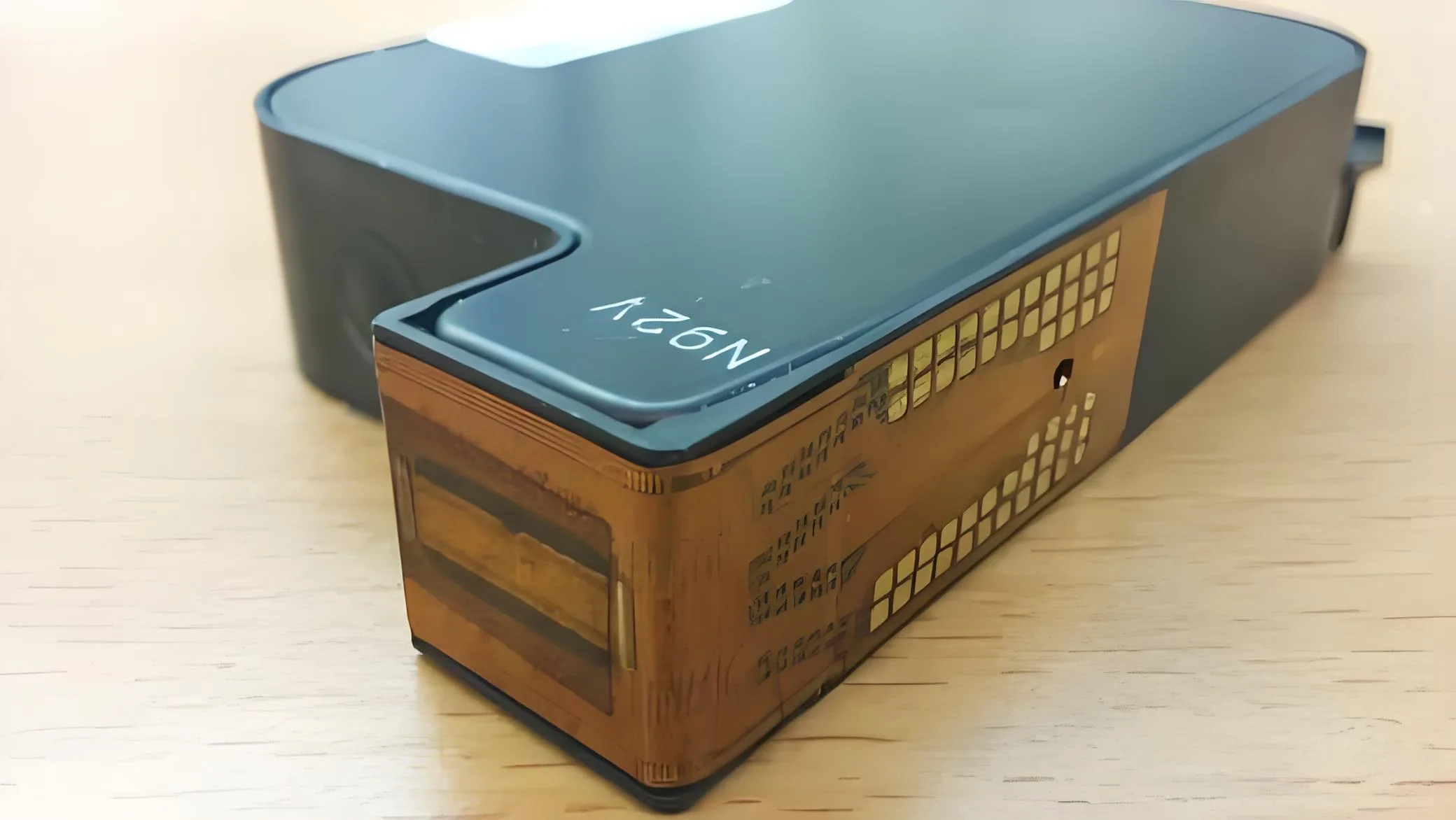
Thermal bubble jet print head
Thermal inkjet technology works by heating small resistive elements to rapidly vaporize the ink and create bubbles, which then propel droplets out of the nozzle at high speed. This process occurs in microseconds, granting thermal inkjet technology the ability to operate at high frequencies and quickly eject ink. Its simple design, faible coût, and self-cleaning feature make it suitable for quick PCB prototyping, solder mask printing, and applications with water-based inks. Cependant, the heating mechanism limits the choice of ink types, mainly to water-based inks, which somewhat restricts its widespread use in PCB manufacturing.
Piezoelectric inkjet technology
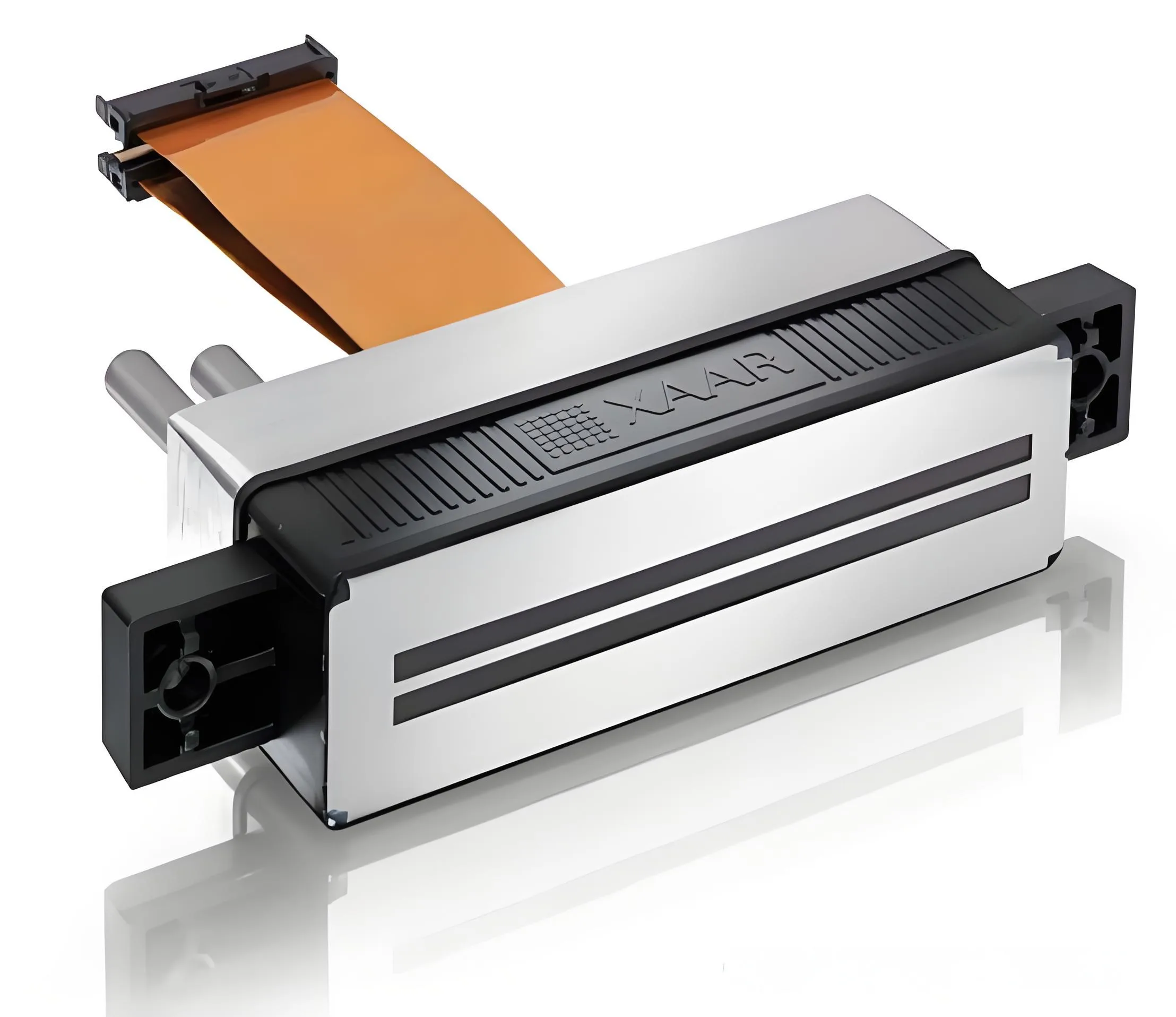
Piezoelectric PCB inkjet print head
Piezoelectric inkjet technology utilizes the piezoelectric effect, where applying voltage causes piezoelectric crystals or ceramics to deform, generating pressure waves that push the ink out of the nozzle. This technology is known for its high precision, long lifespan, and broad ink compatibility, capable of handling a variety of ink types including solvent-based, UV-curable, and conductive inks. The high resolution (up to 2880dpi) and grayscale printing capability of piezoelectric print heads make them excellent for printing fine conductive lines, complex circuit patterns, and precise material deposition.
Which Is Superior?
In the field of PCB manufacturing, both thermal bubble and piezoelectric inkjet technologies have their focuses and jointly drive the development of the industry.
Thermal Bubble Inkjet
With its high jetting frequency (up to 15000Hz) and lower cost, it becomes an ideal choice for rapid PCB prototyping and mass production of water-based solder masks. Despite limitations in ink types, thermal bubble inkjet technology can still handle tasks such as printing solder masks, depositing label graphic inks, and coating and adhesives in batches. Its self-cleaning ability ensures long-term stable printing quality.
Piezoelectric Inkjet
With its high precision, longevity, and wide ink compatibility, it exhibits outstanding performance in printing fine conductive lines, complex circuit patterns, special coating materials, and precise control of adhesives and solder pastes. Piezoelectric inkjet technology can handle functional inks like conductive materials and nanoparticles, and through grayscale printing technology, it can accurately control ink droplet size to achieve gradient thickness or adjust line conductivity uniquely. This flexibility makes it the preferred choice for advanced PCB manufacturers like UGPCB in PCB production and electronic device additive manufacturing processes.
Comparative Analysis: The Art of Choice
In PCB manufacturing, the choice between thermal bubble and piezoelectric inkjet technology depends on specific application needs.
Print Quality and Precision
Piezoelectric printheads, with a resolution of up to 2880dpi, far surpass the 1200dpi of thermal bubble inkjet, enabling finer conductive line deposition and complex designs.
Ink Compatibility
Piezoelectric inkjet technology can handle various ink types, including conductive inks and large particle metal inks, offering more possibilities for advanced PCB manufacturing processes. Thermal bubble inkjet is mainly limited to water-based and specific emulsion inks.
Durability and Lifespan
Piezoelectric printheads usually have a longer service life due to reduced thermal stress, suitable for long-term stable operation. Thermal bubble printheads may need more frequent replacement due to their heating mechanism.
Cost Consideration
Thermal bubble inkjet technology has an advantage in cost control due to its simple design and low cost. Cependant, the longevity and multifunctionality of piezoelectric printheads can offset their higher initial costs over time.
Printing Speed and Environmental Friendliness
Thermal bubble inkjet technology can achieve fast PCB character printing with its high-frequency jetting capability. It is also compatible with water-based inks, conducive to environmentally friendly manufacturing. Piezoelectric inkjet technology, though slightly slower in printing speed, offers extensive ink compatibility allowing for environmentally friendly formulations when needed.
Conclusion: Perfect Fusion of Technology and Needs
On the vast stage of PCB manufacturing, both thermal bubble and piezoelectric inkjet technologies play indispensable roles. Thermal bubble inkjet, with its efficiency and economy, is suitable for standard PCB mass production; while piezoelectric inkjet technology, with its high precision and versatility, becomes the preferred choice for high-end and complex PCB prototyping manufacturing. Ensemble, they complement each other, driving continuous innovation and development in PCB manufacturing technology.
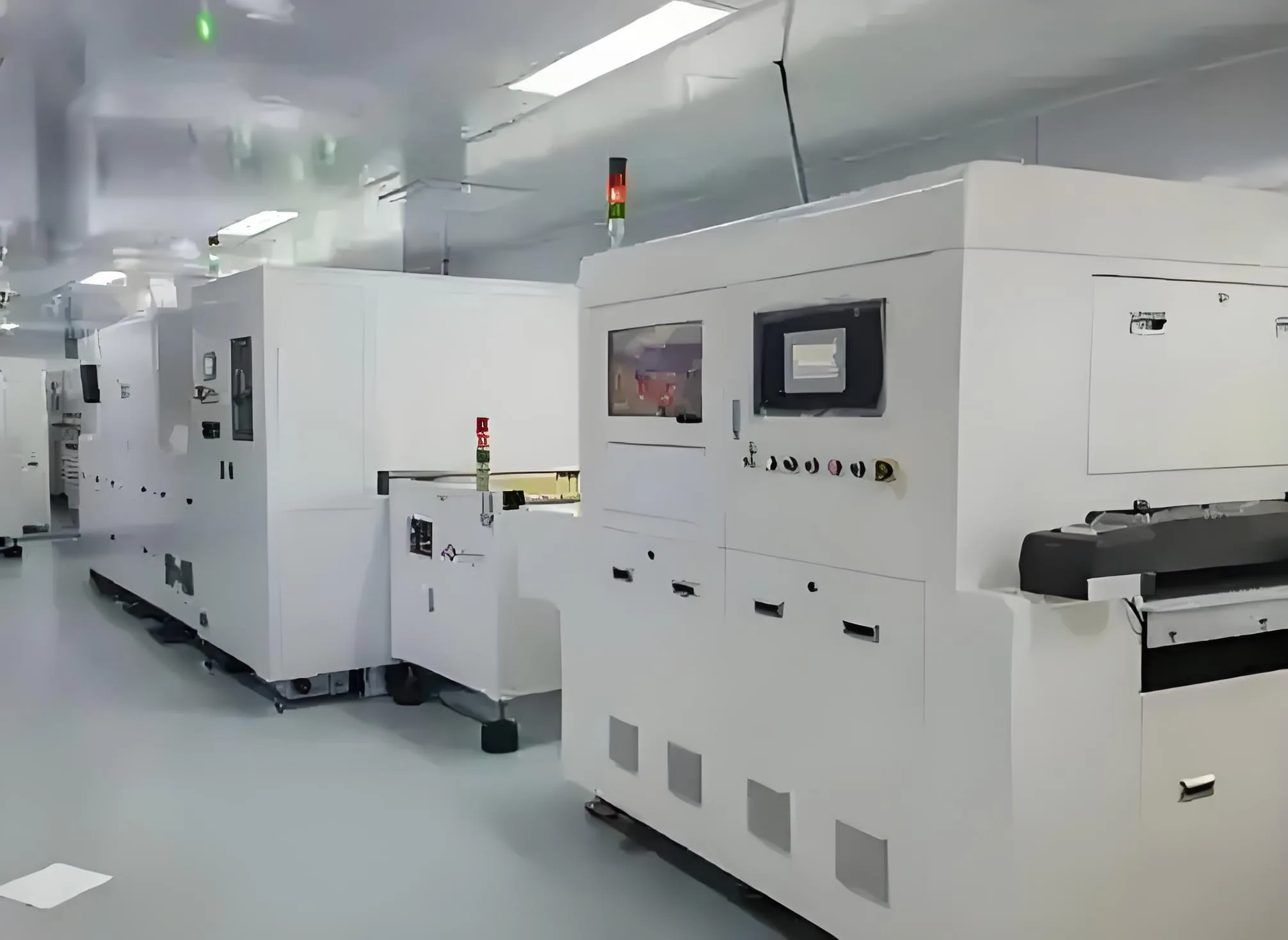
Character Printing Workshop of UGPCB
In the future of PCB manufacturing, as technology continues to advance and application demands become increasingly diverse, thermal bubble and piezoelectric inkjet technologies will continue to leverage their unique advantages, leading the industry towards higher levels. Whether pursuing efficiency in rapid mass production or exploring the possibilities of fine and complex designs, inkjet technology will shape a smarter and more efficient new era in PCB manufacturing with its endless creativity.