S1150GH features
– Lead-free compatibility and excellent ion migration resistance
– 低いZ軸熱膨張係数
– ハロゲンフリーPCB, antimony-free, red phosphorus free, and no other highly toxic and residual toxic components during waste combustion
– Applicable to high-end HDI performance processing requirements
S1150GH application field
– 家電
– スマートフォン, 錠剤, ラップトップ
– LED, Game device
S1150GH PCB Material
Halogen-free PCB Material Shengyi S1150GH
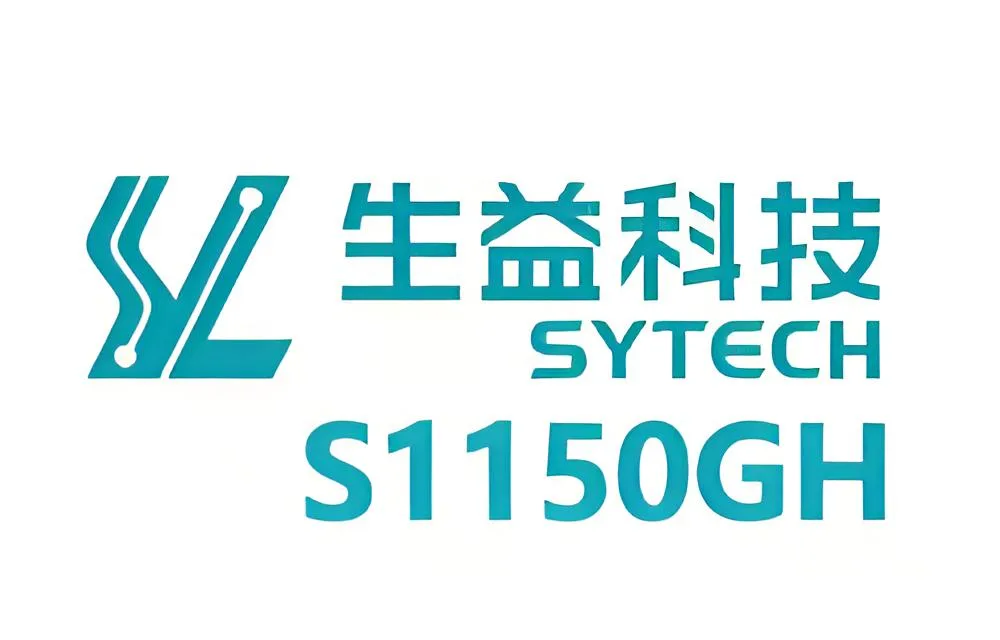
Halogen-free PCB material of Shengyi S1150G.
PCB material for halogen-free high reliability multilayer board: S1150GH+prepreg: S1150GHB PCB manufacturing precautions
1. S1150GH/S1150GHB storage conditions
1.1 S1150GH/S1150GHB copper clad plate
1.1.1 保存方法
Put it on the platform or suitable rack in the original packaging form to avoid heavy pressure and prevent deformation of the plate caused by improper storage.
1.1.2 保管環境
プレートは換気の良い場所に保管してください。, 直射日光を避け、乾燥した室温環境, rain and corrosive gas erosion (the storage environment directly affects the plate quality). Double panels should be stored in a suitable environment for two years, and single panels should be stored in a suitable environment for one year. 内部性能はIPC4101規格の要件を満たすことができます。.
1.1.3 手術
Wear cleaning gloves to handle the plate carefully. 衝突, スライディング, 等. 銅箔を損傷します, 素手で操作すると銅箔表面が汚れます。. これらの欠陥はプレートの使用に悪影響を与える可能性があります。.
1.2 半硬化シート
1.2.1 保存方法
Store horizontally in the original packaging form to avoid heavy pressure and damage of the semi curing sheet caused by improper storage. The remaining roll shaped semi curing sheet after cutting shall be sealed and packed with fresh film and put back on the bracket in the original packaging.
1.2.2 保管環境
プリプレグは、紫外線の当たらない環境で密封パッケージに保管する必要があります。. 具体的な保管条件と保管期間は以下の通りです。
状態 1: 温度<23 ℃, 相対湿度<50%, 保管期間 3 月,
状態 2: 温度<5 ℃, 保管期間 6 月,
The relative humidity has a great influence on the quality of the prepreg, and the corresponding dehumidification treatment should be carried out in humid weather. It is recommended to use the prepreg within 3 days after unpacking.
1.2.3 切断
It is better for professionals to wear clean gloves for cutting to prevent the surface of the prepreg from being polluted. プリプレグにしわが寄らないように注意して作業する必要があります。. When PP is cut, the worktable should be cleaned first to avoid cross contamination of different types of PP resin powder.
1.2.4 予防
プリプレグを冷蔵倉庫から取り出したところ, パッケージを開ける前に温度回復プロセスを経る必要があります. 温度回復時間は以上です 8 時間 (特定の保管条件に応じて). The package can be opened after the same temperature as the ambient temperature. The prepreg that has been opened into sheets must be stored in Condition 1 または条件 2 そしてできるだけ早く使い切ってください. After more than 3 日, インジケーターが適格になった後に再チェックして使用する必要があります. After the roll shaped prepreg is opened, the remaining roll shaped mantissa shall be used, It is required to carry out sealed packaging of the original packaging degree and store it in Condition 1 または条件 2. IQC検査計画がある場合, the prepreg shall be tested as soon as possible after receipt (以上ではありません 5 日) IPC-4101規格に準拠. If the prepreg is dehumidified before use, it is recommended to set the conditions for the dehumidification cabinet: 温度<23 ℃, relative humidity about 40%, and the upper limit of fluctuation shall not exceed 50%.
2. S1150GH/S1150GHB PCB processing suggestions
2.1 切断
切断には鋸盤を使用することをお勧めします, 続いてシャーリングマシン. Note that cutting with roller knife may cause plate edge delamination, so as to avoid plate edge delamination due to tool wear and improper clearance.
2.2 コアプレートのベーキング
According to the actual use situation, the core plate can be baked. If the core plate is baked after opening, it is recommended that the core plate be baked after a high-pressure water wash after opening to avoid the introduction of resin powder produced during the shearing process to the plate surface, エッチング不良の原因となる可能性があります. It is recommended that the core plate be opened and baked at 150 ℃/2~4h. プレートは熱源に直接接触できないことに注意してください。.
2.3 Browning of inner layer
S1150GH scheme is suitable for browning process.
2.4 スタッキング
積層プロセスでは、ボンディングシートの積層順序が一貫していることを保証する必要があります。, and the overturning action shall be avoided during the stacking process to reduce the problems such as warping, deformation and folding caused thereby.
The time from browning of core plate to pressing plate shall be controlled within 12 時間. When the buffer material may have moisture absorption risk, it is recommended to dry it.
Due to the material characteristics, it is easy to carry static electricity. When stacking, pay special attention to the adsorption of foreign matters on PP.
In order to ensure good alignment effect of expansion and contraction during plate arrangement, it is recommended to use rivet riveting for fixation. If fusion is required, it is recommended to use electromagnetic heat fusion. 同時に, the best fusion effect parameters should be evaluated in detail. For other fusion methods, the PCB’s own conditions should be carefully evaluated for fusion effect to avoid layer deviation caused by poor fusion.
2.5 ラミネート加工
It is recommended to select the press plate with good vacuum pumping performance and vacuum valve sealing to avoid the entry of external moisture.
The recommended heating rate is 1.5~2.5 ℃/min (the material temperature is within the range of 80~140 ℃).
It is recommended that the laminating pressure be 350-430psi (油圧プレス). The specific high pressure should be adjusted according to the structural characteristics of the plate (プリプレグの枚数と接着剤充填領域のサイズ). It is recommended to turn to high pressure at 80-100 ℃.
Curing conditions: 温度 180 ℃, time more than 60min.
Cooling rate < 2 ℃/min.
The material temperature of hot pressing is less than 150 ℃.
If copper foil heat conduction press is used, Shengyi Company shall be informed in advance.
多層基板に絶縁板や単板を使用する場合, 断熱ボードまたは単一パネルは、滑らかすぎる断熱ボードによって引き起こされる不十分な接着力を避けるために、使用する前に粗面化する必要があります。, または、両面基板を単一パネルまたは絶縁基板にエッチングして生産することもできます。.
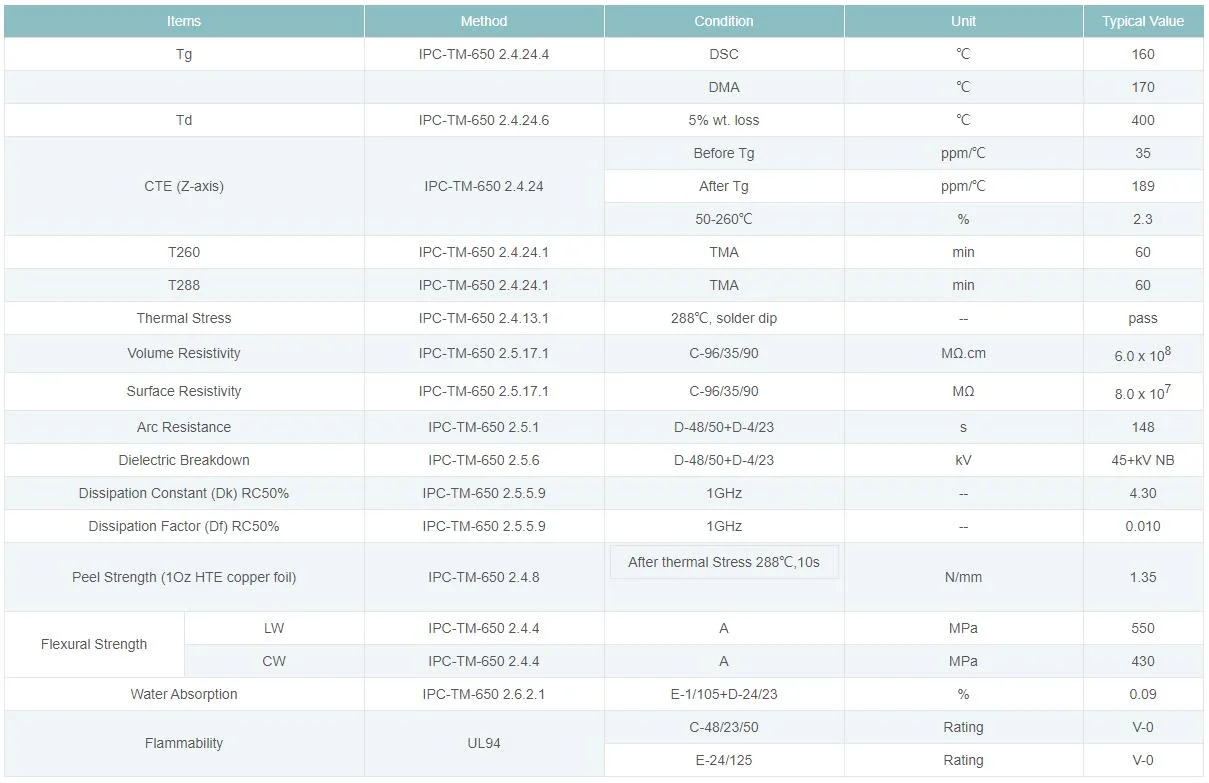
Shengyi S1150G Halogen-Free PCB material Specifications Table
2.6 掘削
It is better to use a new drill.
The stack thickness is recommended to be no more than 2 pieces/stack (calculated as per the plate thickness of 1.6mm/block).
It is recommended to limit the drilling hole to 1000-2000 holes.
The feed rate for drilling shall be 15-20% lower than that for processing ordinary FR-4 materials.
2.7 Drying plate after drilling
It is suggested that the drying conditions after drilling should be 170-180 ℃/3h. Note that the plates should not be in direct contact with the heat source.
Baking before resin plug hole after back drilling: 170-180 ℃/2-3h.
2.8 Dirt removal
It is suggested that the specific parameters should be set according to the actual PCB structure (board thickness, aperture size), and all kinds of structural boards should be fully evaluated in detail to determine the best matching glue removal conditions and parameters. The glue removal effect should refer to the fact that there is no resin residue at the copper junction of the inner layer. The horizontal Desmear or vertical Desmear is recommended. The specific glue removal conditions are related to the equipment, liquid medicine model, board thickness or hole area. Under the premise of full load, the thicker the board is recommended, The longer the degumming time is.
2.9 Solder resistance ink
It is recommended that the drying plate before green oil: 130 ℃/2-4h,
ラックをベーキングに使用する場合, ラック挿入時にプレートが圧迫されたり変形したりした場合, 焼成後に反りが発生します. It is not recommended to back wash the solder resist ink, which may cause white spots.
2.10 錫溶射
It is suitable for lead-free tin spraying process. For the structure of thick copper and large copper surface on the outer layer (or thick copper plating), the temperature is high during lead-free tin spraying, resulting in excessive thermal stress, which is prone to white spots between large copper surfaces, copper skin warping and other problems. The improvement measures are as follows:
1. Try to reduce the tin spraying temperature, shorten the tin spraying time, and reduce the thermal stress generated during tin spraying,
2. Before tin spraying, pre bake the plate under the condition of 140-150 ℃/2h, and spray tin immediately to remove the moisture accumulated on the plate surface, which can reduce the probability of white spots,
3. Avoid too large tin spraying surface, or increase the thickness of green oil appropriately, which can well cushion the thermal stress generated during tin spraying,
4. The large copper surface structure is designed as a grid structure.
2.11 プロファイル処理
It is recommended to use a milling machine for processing and reduce the traveling speed appropriately. It is not recommended to use a beer plate for processing.
2.12 包装
It is recommended to bake the plate before packaging under the condition of 120 ℃/4-6h to avoid heat resistance degradation caused by moisture. Aluminum foil vacuum packaging is recommended.
3. S1150GH/S1150GHB welding
3.1 包装の有効期限
It is recommended to use vacuum aluminum foil bags for packaging, and the recommended period of validity is 3 月. コンポーネントをベイク処理する方がよいでしょう。 120 ℃ for 4~6h before assembly.
3.2 S1150GH/S1150GHB reflow welding parameters
Suitable for conventional lead-free reflow soldering process.
溶接温度は350~380℃です。 (using temperature controlled soldering iron),
単一溶接点の溶接時間: 内で 3 秒.