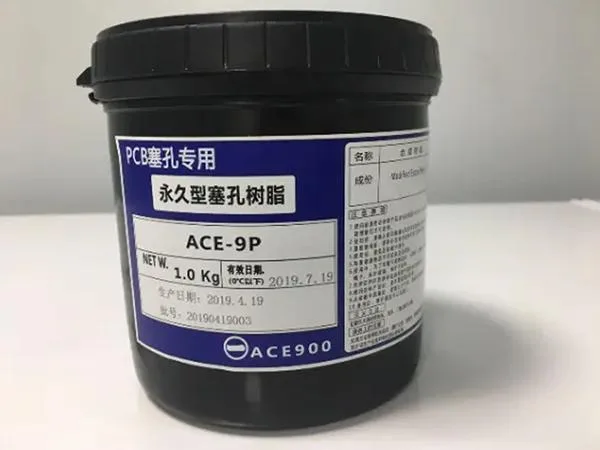
PCB 용 수지 플러그
전자 제조의 광대 한 우주에서, 인쇄 회로 기판 (PCB) 의심 할 여지없이 가장 밝은별로 서 있습니다, 전자 장치의 마음과 영혼을 운반합니다. PCB 제조와 관련된 무수한 프로세스 중, 단순 해 보이지만 매우 중요한 것은 PCB 수지 플러그입니다.. 이 프로세스는 회로 보드의 신뢰성과 안정성을 조용히 보호합니다.. 이 기사는이 기술에 대한 깊은 다이빙을 할 것입니다., 신비한 베일을 공개하십시오, 전자 제조에서 독특한 매력을 높이 평가합니다.
나. PCB 수지 플러깅: 프로세스의 기원
PCB 수지 플러깅, 이름에서 알 수 있듯이, PCB의 관통 구멍에 수지 재료를 정밀하게 주입하여 이러한 개구부를 효과적으로 밀봉하는 작업이 포함됩니다.. 이 과정의 목적은 솔더 페이스트가 구멍을 통해 보드 뒷면으로 스며들지 않도록하는 것입니다., 따라서 단락의 위험을 피합니다. 전통적인 잉크 플러깅과 비교합니다, 수지 재료 (에폭시) 우수한 신뢰성으로 인해 이상적인 솔루션이되었습니다., 프로세스 적응성, 및 재료 특성.
ⅱ. 프로세스 흐름: 정밀도와 예술의 조합
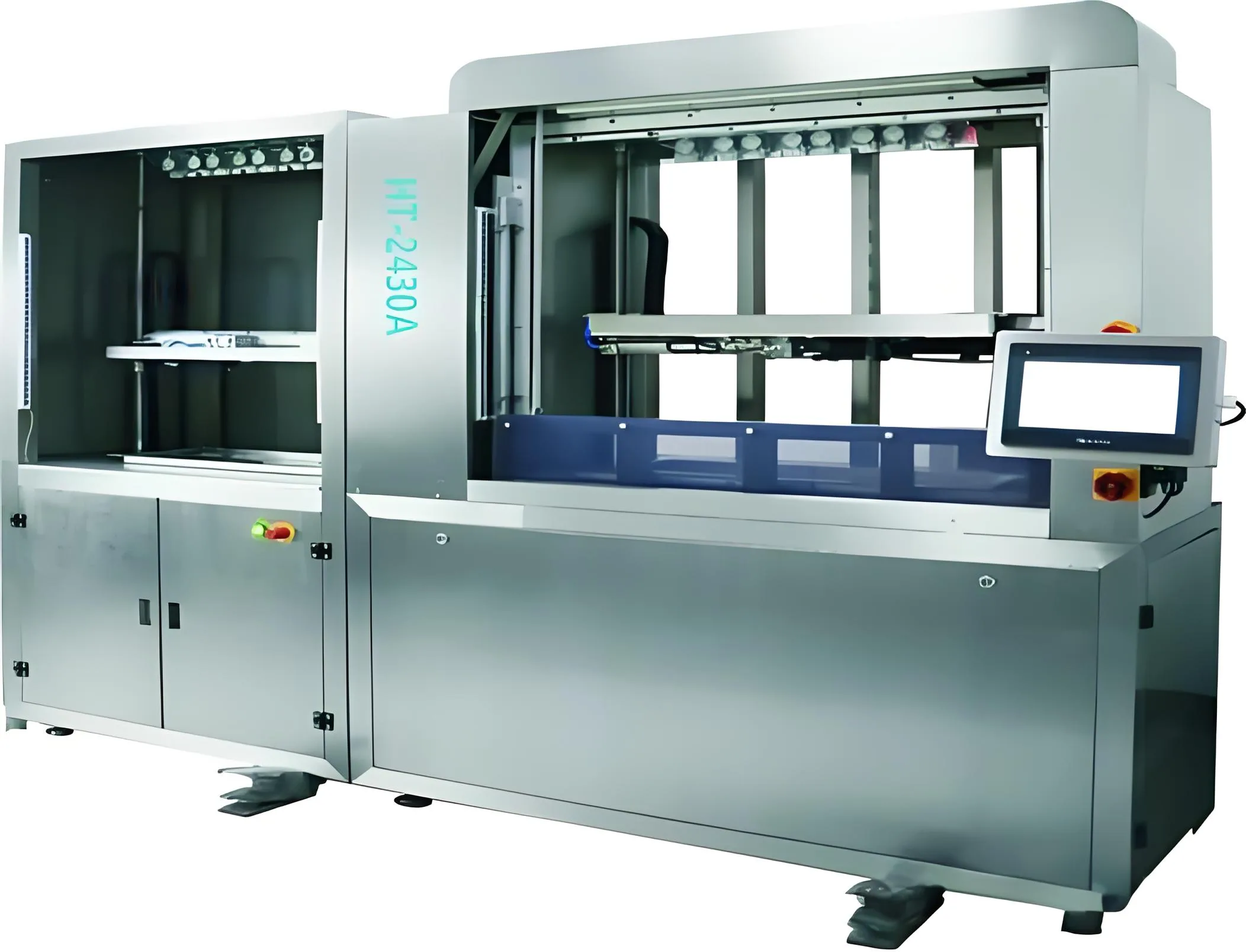
PCB 수지 플러그 기계 장비
1.구멍 처리
초기 수지 플러그 공정에는 복잡한 구멍 처리 단계가 포함되지 않았습니다.. 하지만, 고온 환경에서 PCB의 적용이 증가하고 열 팽창 계수의 지속적인 감소로 (CTE) 보드, 수지의 확장 계수와 보드 재료의 불일치가 점차 명백 해졌습니다.. 이 문제를 해결하기 위해, 현대 공정에는 수지와 보드 재료 사이의 결합 강도를 향상시키기 위해 구멍 벽의 거친 또는 마이크로 에칭 단계가 포함됩니다., 구멍 벽으로부터 수지 분리의 위험을 줄입니다.
2.플러그
업계는 일반적으로 플러그 작업을위한 스크린 인쇄를 채택합니다. 하지만, 자동차 및 항공 전자 제품과 같은 고 주문형 제품, 진공 플러그 장비가 선호됩니다. 수평 및 수직 진공 플러그 머신 각각은 특성이 있습니다.; 전자는 넓은 지역에 적합합니다, 균일 성 반복 작업, 후자는 작은 지역에 더 적합합니다, 고정밀 플러그 작업.
3.빵 굽기
막힌 후, 고온 베이킹 과정 150 섭씨도 1 수지가 완전히 치료되고 안정적인 절연 층을 형성하는 데 시간이 필요합니다.. 이 단계는 플러그의 품질을 보장하고 수지 재료가 최적으로 수행 할 수 있도록하는 데 중요합니다..
4.수준 측량
막힘 후 수지가 보드 표면 위로 약간 튀어 나오기 때문에, 연마 벨트 또는 세라믹 브러시를 사용하여 표면을 매끄럽게 갈아야합니다. 후속 프로세스가 부드럽게 진행되도록. 이 과정에서, 고르지 않은 구리 두께 또는 큰 구멍의 과도한 절단을 피하기 위해 연삭 방향을 여러 번 변경해야합니다..
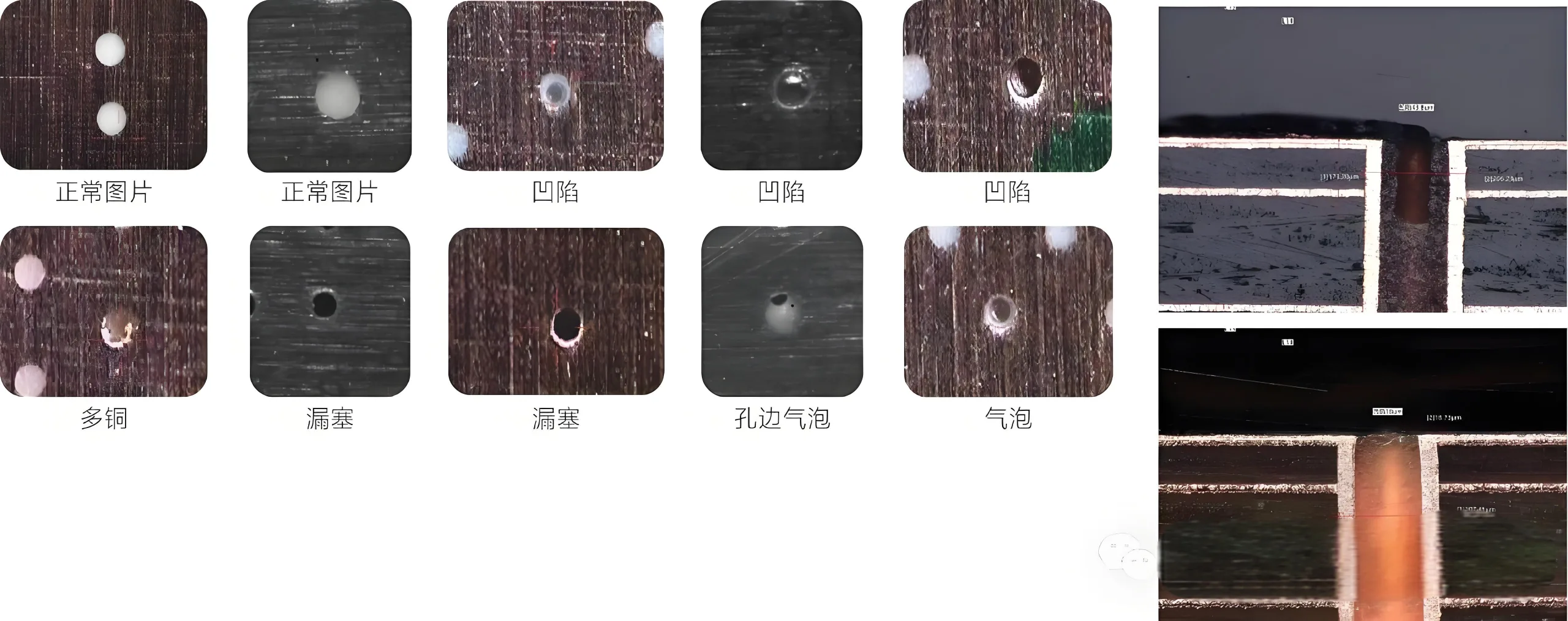
PCB 용 수지 플러그
III. 장점: 성능 및 효율성의 이중 향상
1.제품 신뢰성 향상
PCB 수지 플러그는 솔더 누출 문제를 효과적으로 해결합니다., 막힘의 균열로 숨겨져있는 오염 및 그 결과 전도성 양극 필라멘트 (CAF) 현상. 산업 데이터에 따르면, 수지 플러그 공정을 사용한 PCB는 신뢰도가 증가한 것으로 나타났습니다. 30% 기존의 잉크 플러그 프로세스와 비교합니다, 제품 수명 및 안정성을 크게 향상시킵니다.
2.신호 무결성 향상
수지 막힘과 신호 무결성 사이에는 밀접한 관계가 있습니다.. 플러그 프로세스를 최적화함으로써, 신호 전송 경로를 개선 할 수 있습니다, 신호 손실 및 간섭 감소. 이 장점은 특히 고주파 전자 장치에서 분명합니다., 고속 신호.
3.부분 밀도 증가
수지 플러그 프로세스는 또한 PCB의 부품 밀도를 증가시키는 유리한 조건을 만듭니다.. 구멍의 충전 및 밀봉을 정확하게 제어함으로써, 제한된 공간 내에서 더 많은 구성 요소를 배열하고 상호 연결할 수 있습니다.. 전자 제품으로 가벼운 경향, 더 작은, 더 통합 된 개발, 이 과정의 중요성은 점점 더 두드러지고 있습니다.
4.기대합니다
수지 막힘 기술을위한 새로운 장
앞을 내다보며, 고밀도에 대한 수요가 지속적으로 증가함에 따라, 고분비 PCB 보드, Resin Plugging 기술은 PCB 제조 분야에서 더욱 중추적 인 역할을합니다.. 한편으로, 재료 과학의 지속적인 발전으로, 새로운 수지 재료의 개발은 플러그 프로세스의 성능과 신뢰성을 더욱 향상시킬 것입니다.. 반면에, 지능형의 도입, 자동화 된 장비는 플러그 프로세스의 생산 효율성 및 품질 관리 수준을 더욱 향상시킵니다..
게다가, 수지 플러그가 고립 된 공정이 아니라 PCB 제조의 다른 측면과 밀접한 관련이 있음을 인식해야합니다., 전자 제품 제조의 완전한 체인 형성. 그러므로, 향후 발전에서, 수지 플러그를 다른 프로세스와 더 잘 통합하는 방법 전반적인 성능을 최적화하는 방법은 업계에서 중요한 주제가 될 것입니다..
결론: 정밀 수호성, 함께 미래를 형성합니다
PCB 수지 플러깅, 겉보기에 간단한 과정, 전자 제조에서 중요한 역할을합니다. 회로 보드 안정성의 보호자 일뿐 만 아니라 향상된 전자 제품 성능의 프로모터이기도합니다.. 향후 발전에서, 우리는 지속적인 기술 진보와 지속적인 혁신으로, 수지 막힘 기술은 전자 제조 분야에서 더 밝게 빛날 것입니다., 인간 기술 발전에 더 많은 기여를합니다.